AP&T Group simplifies their resource planning process by substituting 3 tools with Float
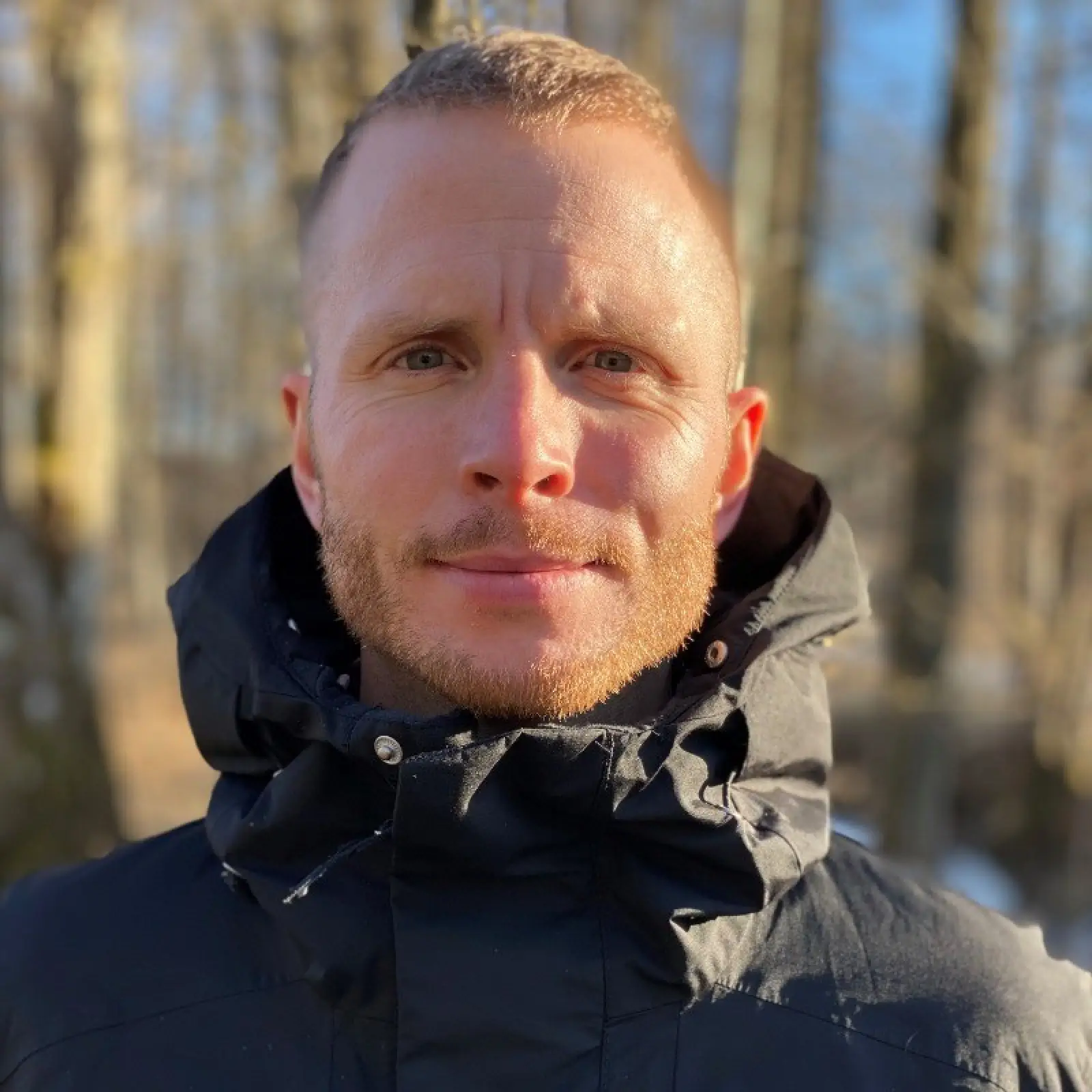
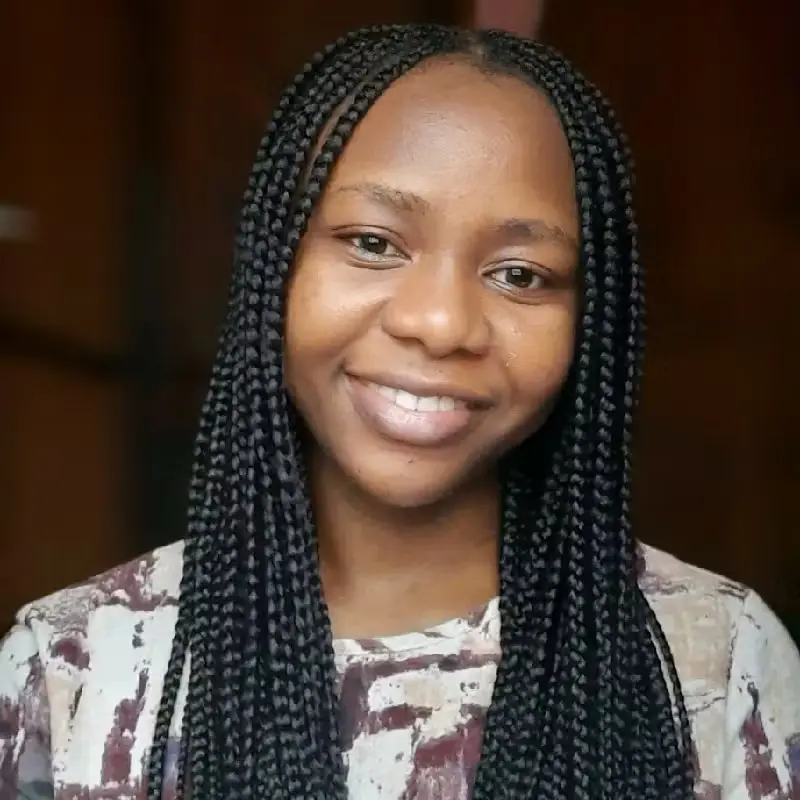
AP&T Group specializes in advanced solutions for sheet metal and fiber forming.
The company, with headquarters, development, and manufacturing in Sweden, has been in operation for over 50 years.
AP&T Group is a global player with customers in diverse industries, including major automotive brands like Toyota, Volvo, Nissan, Fiat, Volkswagen, and Lucid. Chances are, vital parts of your car were manufactured using technology and equipment from AP&T Group.
With so many moving parts, the company uses Float to make smarter resourcing decisions and deliver client projects.
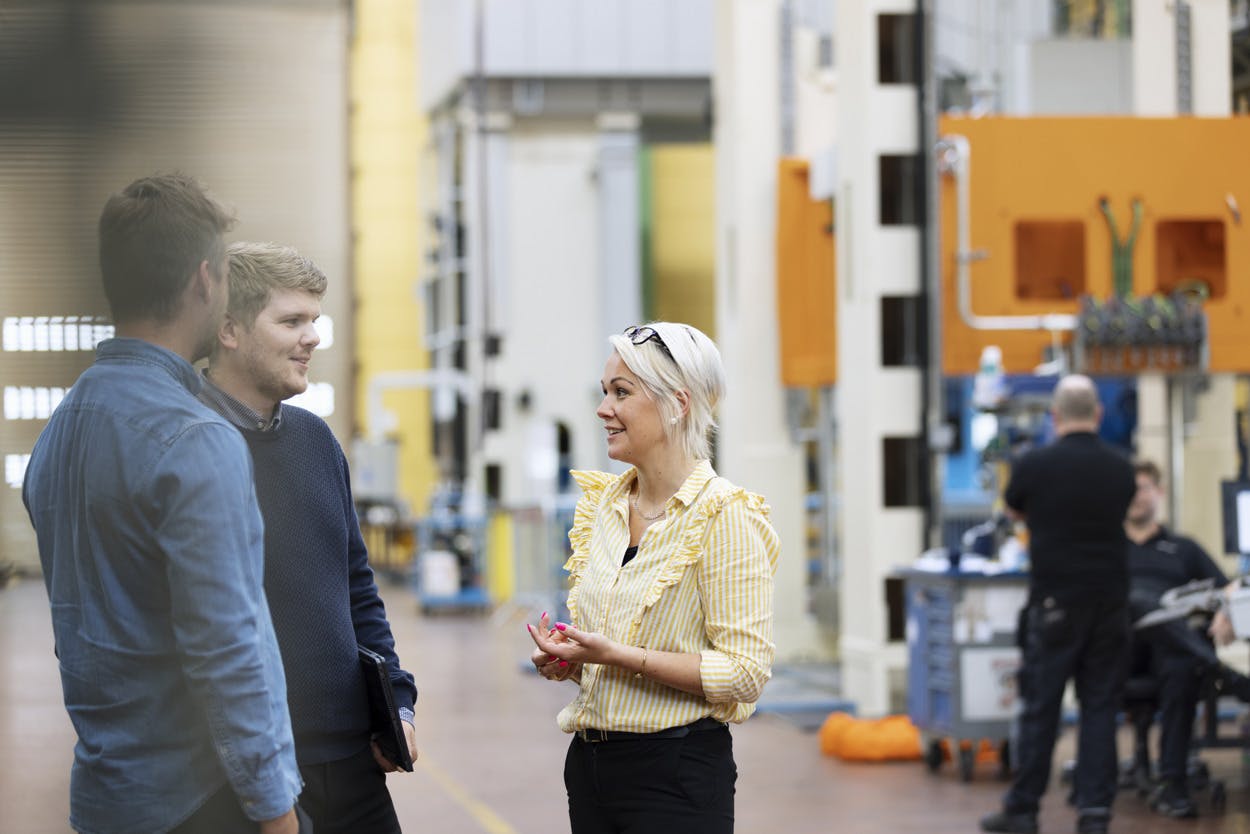
The challenges: disparate resource planning in 3 different tools
At AP&T Group, projects are complex, involving several departments with over 200 people working on metal or fiber forming. Sometimes, projects can last up to two years.
Resource planning was managed through three tools: Microsoft Excel, Microsoft Projects, and a homegrown SQL database system that enabled the team to schedule time for projects. Linus Hall, AP&T Group’s Planning and Logistics Manager, told us:
Every manager wants to do things in their own way. This made life hard for my team and me because we had to consider 17 different perspectives to form a unified plan. To complicate matters, we used three systems for planning– Microsoft Excel, Microsoft Project, and a custom SQL database system developed by one of our engineers.
On top of that, every manager had administrative rights and frequently made changes to resource plans.
“Everyone has their own agendas. They have their own perspective of an issue or how the business should be run. All people always think that their task is the most important in the company,” explains Linus.
All these factors made it very difficult for Linus to get everyone to work towards the same goal.
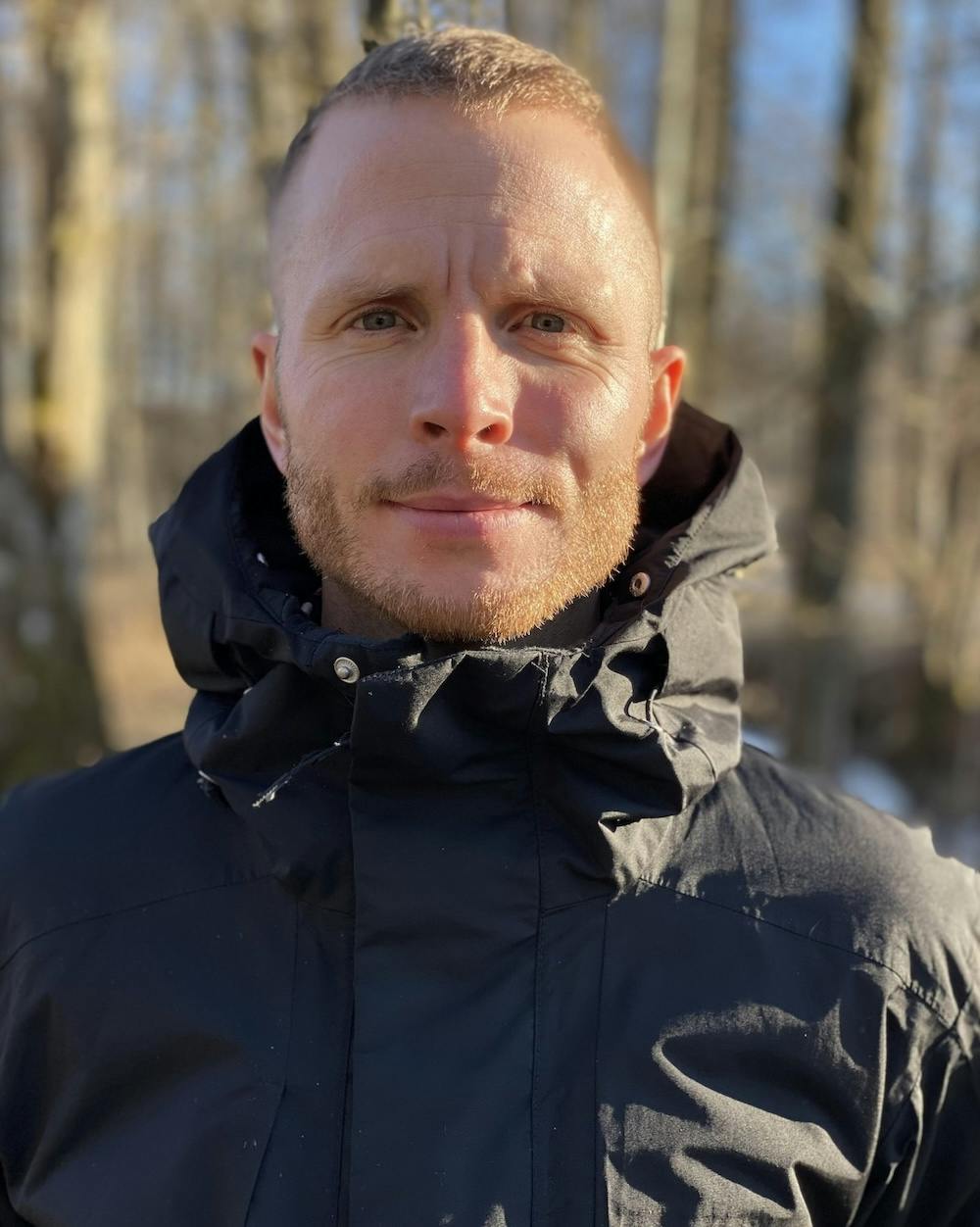
The solution: centralized resource planning in a single tool—set up in less than 6 months
Linus knew the only way forward was to switch to a dedicated resource planning software that would offer a unified, big-picture view of all the projects running at AP&T Group.
While searching for resource planning software, Linus came across Float.
Though impressed by our product, he decided not to use it immediately because the timing wasn’t right. AP&T Group was already implementing an enterprise resource planning system; switching to a resource planning tool as well meant Linus and his team would need to do an overwhelming amount of change management. He decided to stick to the SQL database and spreadsheets for a little longer.
A few months later, a colleague in another division suggested using Float for resource planning. The pain was obviously being felt by more people than just Linus! He went back to evaluating Float, and the team was convinced it could be the right tool for them. They decided to start a project in Float in June. By August, three different departments were using it. By December, they had completely moved their resource planning into Float.
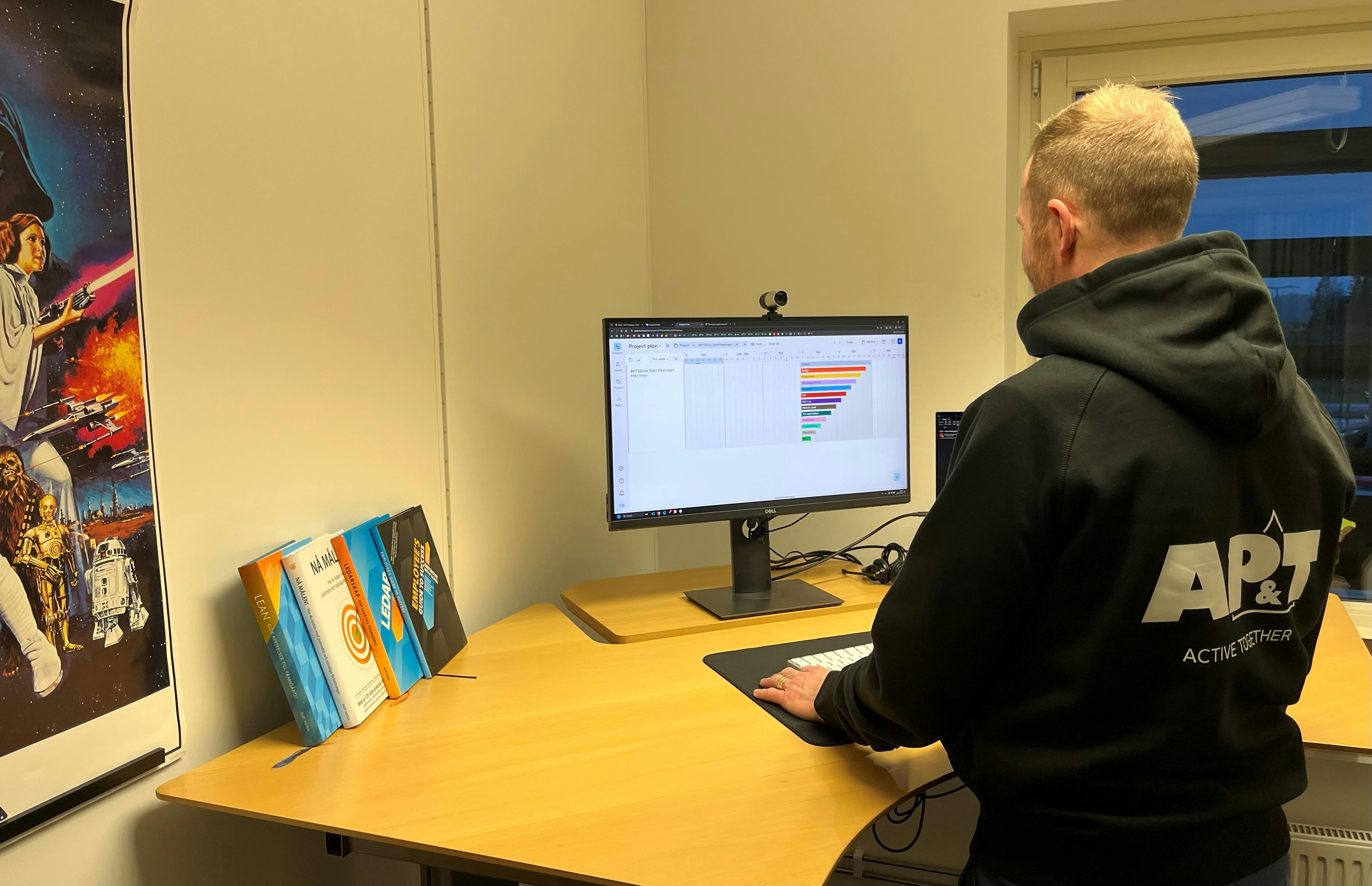
The switch to Float was welcomed by the departments in AP&T Group because it got the job done. Not only did the tool solve the major pain points the team had been experiencing; its impact was also immediately clear to the vast majority of employees, and eventually everybody was won over.
When you roll out a new tool, it’s always difficult to get everyone on board. But I would say 80% really loved Float immediately and they understood it. And the people who didn’t like it at the start are now saying “This tool is so good. Wow.”
The results: one single source of truth for resource plans
Resource planning at AP&T Group no longer happens across disparate tools and siloes between departments have been eliminated.
Float’s schedule provides a unified view of all departments, their engineers’ capacity, and project timelines, which enables managers to collaborate better. They can now coordinate work so that dependent tasks are delivered on time and do not hold the production line from moving forward. Managers can also get context around people’s availability at a glance and get help from another team when they are overstretched.
As an added bonus, managers can spot when engineers are underallocated and assign work to them.
A major benefit for managers is the ease of use and the ease of grasp. You could plan in so many different ways. You could either just drag and drop or duplicate. You could right-click or you could use your short keys. There are so many different ways of doing it and it’s so simple.
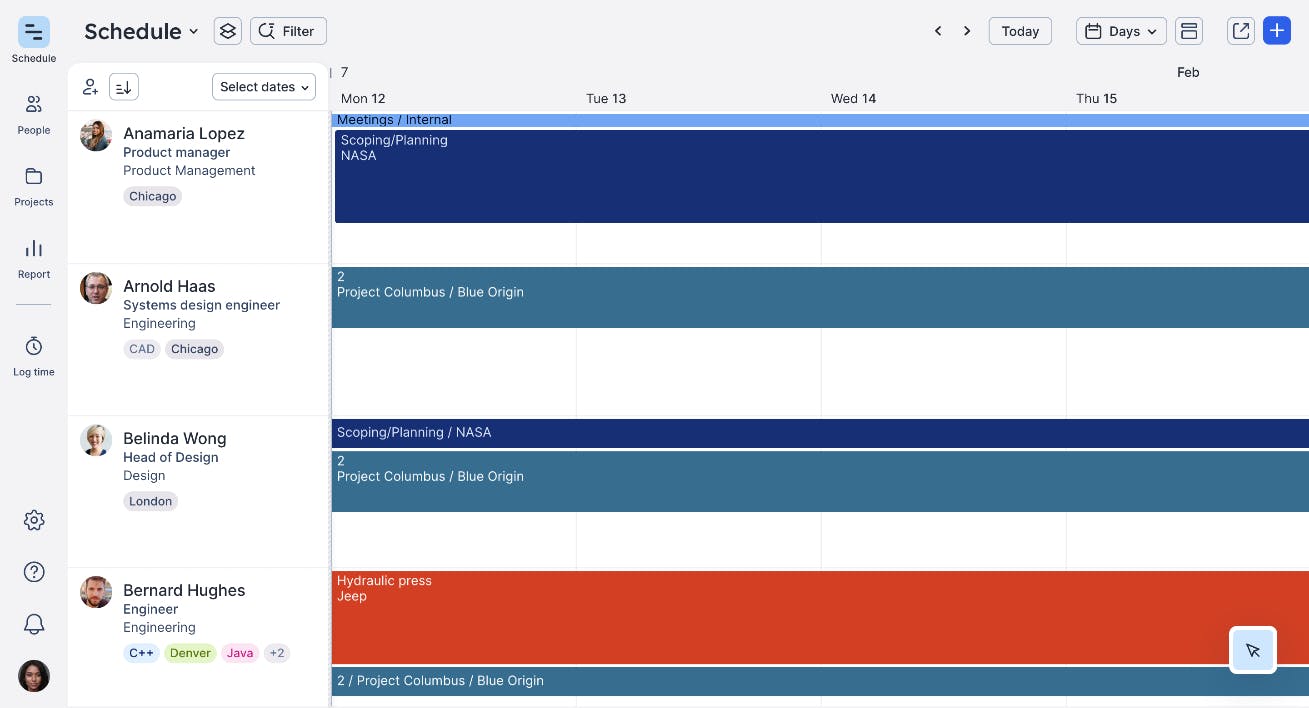
Everybody has been won over—especially the CTO
One unexpected benefit Linus shared with us is that the CTO of AP&T Group finds Float critical to his day-to-day work. To quote Linus, “Our CTO said it’s invaluable in getting a good overview of projects. He can go into the tool and understand what is happening in his function and with his team. Supporting and prioritizing between R&D projects and our customer projects is easier.
In the future, AP&T Group plans to start using Float for planning and logging time spent on tasks.
Float is faster. It is easier. And we get a good overview of our resources.